Posted on January 9, 2023
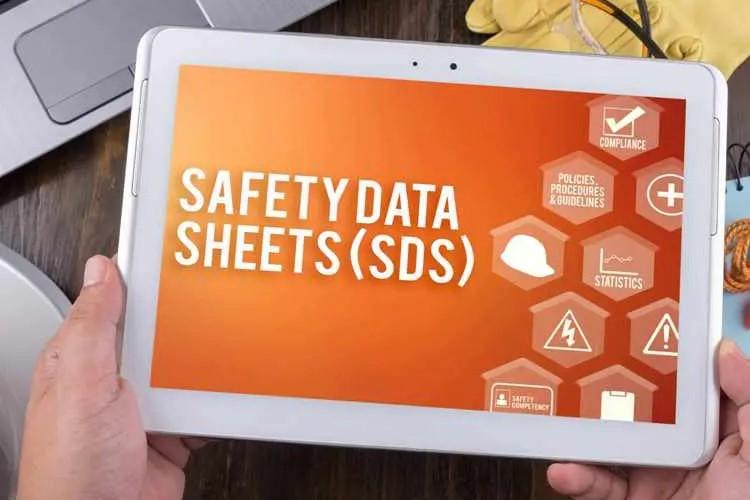
- What is a Safety Data Sheet?
- What Chemical Products Require an SDS?
- Understanding a Safety Data Sheet
- Is an SDS All That Chemical Products Require?
- Seatex Is Experienced in Creating & Maintaining SDSs
- Sections 1-3: Identifying the chemical and understanding its safety risks
- Sections 4-6: Dealing with emergencies
- Section 7-11: Preventing hazardous situations
- Sections 11 & 12: Describing the effects of the chemical on people and the environment
- Sections 13 & 14 (non-mandatory): Explaining how to move the chemical
- Sections 15 (non-mandatory) & 16: Making room for additional information
If your business involves the use of chemicals, you’re bound to come across a safety data sheet (SDS) at some point. When that happens, it will be your legal and ethical responsibility to ensure that everyone on your team who will be working with an SDS-accompanied chemical is trained to do so safely.
With its first aid recommendations, hazard warnings, protective equipment guidance, and more, the SDS is your most valuable teaching tool for doing so.
In addition to some background and context on the subject, in this article you’ll find a plain-language explanation of the contents of an SDS, accompanied by snapshots of a real version of an SDS created by Seatex for one of our products.
What is a Safety Data Sheet?
In 2003, the United Nations (UN) adopted the Globally Harmonized System of Classification and Labeling of Chemicals (GHS). The GHS includes criteria for the classification of health, physical, and environmental hazards, as well as specifying what information should be included on labels of hazardous chemicals as well as the Safety Data Sheets (SDSs) previously known as Material Safety Data Sheets (MSDSs).
OSHA (Occupational Safety and Health Administration) published a proposed rulemaking on September 30, 2009 to align OSHA’s Hazard Communication Standard (HCS) with the GHS by 2012. The GHS requires all owners of the SDS to conform to a specific format of thirteen mandatory sections and three non-mandatory sections organized in a certain order.
An SDS is a detailed document required by OSHA’s Hazard Communication Standard (HCS) 1910.1200 and Lab Safety Standard 1910.1450 to accompany any hazardous chemical. It conveys critical information for the safe handling and use of the chemical, as well as how to respond to the various hazards it poses.
The SDS may come from the manufacturer as a hard copy or in digital format, either before the chemical shipment arrives or with the chemical order. You may elect to keep it in either format, but whichever you choose, the SDS must be readily available to your workers in the work area, not locked up or put behind a password on a computer.
If for some reason the SDS has not been sent with a chemical, you should be able to download it from the manufacturer’s website or request a copy directly.
If you need to store many SDSs, companies like Chemwatch offer online databases for easy cataloging and access.
What Chemical Products Require an SDS?
Any chemical whose manufacturer has determined qualifies under the HCS definition as “hazardous”–meaning it represents a physical or health hazard–requires a safety data sheet.
To determine this, the manufacturer should conduct a hazard evaluation. For example, drugs are potentially hazardous chemicals, so pharmaceutical companies should always conduct a hazard evaluation for their products.
Other types of products that typically have an SDS include:
- solvents
- lubricants
- paints
- cleaners
- sealants
- compressed gasses
- fuels
Although SDSs are not intended for consumers, home products that contain hazardous chemicals may be of interest to members of the public seeking information about a product’s manufacturer, composition, hazards for the people who work with it, etc.
And as OSHA points out, sometimes manufacturers, for various reasons, opt to produce an SDS for non-hazardous chemicals. Because this can be confusing to downstream users, in those instances, the Administration recommends the SDS clearly state that the chemical at issue is not required to have an SDS.
Understanding a Safety Data Sheet
An SDS can seem daunting to read, but it can be broken down into a handful of objectives that we have outlined below:
Sections 1-3: Identifying the chemical and understanding its safety risks
The first few sections of the SDS are intended to make clear what product the handlers are dealing with and what potential dangers they face if something goes wrong.
This way, you can tell by a glance at Page 1 what happens if a certain chemical gets on skin, in eyes, in lungs, swallowed, etc. These statements will be accompanied by up to eight pictograms or symbols that correspond to the respective hazards.
You’ll also be able to learn from these sections the manufacturer’s contact information and details about the chemical itself, such as its:
- Chemical Abstracts Service (CAS) Registry Number
- name
- formula
- weight
- recommended use
- composition concentration, although this may be withheld as a trade secret. As you can see in our example, we have included the required statement indicating we are withholding the concentration as a trade secret.
Sections 4-6: Dealing with emergencies
With the potential hazards laid out, the SDS now seeks to tell you, the reader, what to do should any of those hazards become a reality. Sections 4 and 6 detail the first aid measures and clean-up measures in the event of a spill, respectively, while Section 5 is intended for use by firefighters.
In recognition of the urgency of this situation, the SDS’ creators should have clearly delineated–such as with bolded text–the various emergency situations that may occur. You should be able to quickly identify the relevant health threat and how to remedy it.
Be sure to check whether there are recommendations as to what safety precautions you as the first aid responder need to take before attempting to render aid. There may also be instructions for physicians, as well, so the SDS should be sent along with the victim should they require a hospital visit.
Section 6 will cover the materials, equipment, and procedures necessary to safely contain the situation. Pay attention to whether there are different recommendations for small and large spills.
In the event of a fire caused by the chemical, Section 5 details what equipment is recommended for both you and firefighters, if they are needed. It also conveys potential hazards of this chemical igniting.
Section 7-11: Preventing hazardous situations
Although a bit counterintuitive, this may be where you want to start reading the SDS as it’s here you’ll learn how to safely handle the chemical, what kind of equipment to use and wear while doing so, and much more detail about the chemical’s properties. Assuming these guidelines are followed, you’ll be much less likely to need the preceding first aid and hazard information.
In addition to stating the chemical’s exposure limits, Section 8 details the arrangements you’ll need to make before working with the chemical, such as:
- PPE (personal protective equipment) (e.g. goggles, gloves, face shield, boots)
- nearby emergency treatment options (e.g. showers, eyewash stations)
- general hygiene instruction for all workers (e.g. no taking contaminated clothing off-site, no food or drinks nearby)
One of the most important themes of this segment of the SDS is reactivity, the situations in which a hazardous chemical becomes even more hazardous. For example, Sections 7 and 10 may both cover the kinds of materials that can’t be used in storage due to reactivity danger.
Similarly, Section 9 covers the physical properties and conditions under which usage of the chemical could become dangerous. The section leads off with a helpful guide to the appearance and odor of the product. Stop engaging with the chemical immediately if the description does not match what you are observing upon inspecting the chemical.
Sections 11 & 12: Describing the effects of the chemical on people and the environment
Here the SDS follows up on the health implications of the chemical by reiterating how someone might be injured via interaction with the chemical, and the immediate, delayed, and chronic effects and symptoms of short- and long-term exposure.
You may see references to “LD50,” which is a way to estimate the chemical’s acute toxicity based on its lethality to test animals. LC50 is another toxicity indicator that estimates lethal concentration of a chemical in air.
Section 11 is also required to state if the chemical is a known or potential carcinogen according to OSHA or select other organizations.
Although not mandatory, Section 12 lays out what can happen if the chemical is released into the environment. This may be test results or other information describing the toxicity for land and aquatic animals and plants, the possibility of leaching into groundwater, the chemical’s biodegradability, and more.
Sections 13 & 14 (non-mandatory): Explaining how to move the chemical
Whether you need to dispose of the chemical or simply transport it somewhere else, you’ll find guidance in these two sections.
Although it may not be explicitly mentioned, both activities should be done in accordance with Section 8’s guidelines on PPE and exposure controls. As these sections are non-mandatory, either or both sections may refer you to the relevant state or federal rules that apply to you, such as those administered by the Texas Commission on Environmental Quality.
If you see a UN Number in Section 14, that is the global group number for a class of chemicals with similar hazardous properties (e.g. UN1993 for most flammable liquids). There may also be a packing group number based on the degree of hazard, an IBC (International Bulk Chemical) Code for bulk transport guidance, or Department of Transportation shipping info if the DoT regulates the chemical.
Sections 15 (non-mandatory) & 16: Making room for additional information
Even though the SDS is an OSHA requirement, the Administration recognizes that some chemicals will also be regulated by other bodies. Section 15 is where it makes room for manufacturers to list these additional groups that have oversight on their chemical. Because it’s not a mandatory section, how detailed the information may be is up to each SDS creator.
In the Seatex example below, we’ve elected to list both international and domestic rules and organizations, whether they apply to this chemical, and if so, how they do.
Although OSHA suggests Section 16 is used to display the latest date of revisions to the SDS, creators often use the section to (also) post a disclaimer to the effect that everything in the SDS is true and accurate to the best of their knowledge, and that the burden is on you to determine if the chemical product is suitable for your purposes.
Is an SDS All That Chemical Products Require?
If it originated outside the U.S. or is sold internationally, a chemical product may have a GHS label on it. Although not required, the Globally Harmonized System of Classification and Labeling of Chemicals is the United Nations’ unified system for streamlining chemical hazard identification throughout the world.
OSHA’s latest SDS requirements have been updated to sync with the GHS, which identifies key info such as the manufacturer/supplier, hazard pictograms and statements, signal words (“warning” or “danger”), and more.
Seatex Is Experienced in Creating & Maintaining SDSs
Seatex is a chemical contract manufacturer that provides a turnkey solution for a given chemical product, including hazardous chemicals, from proof of concept through to manufacturing, packaging, and shipping.
We create and maintain a comprehensive library of SDSs so that our customers and anyone downstream who comes into contact with our hazardous chemicals has the information they need to stay safe.
Category: EDUCATION